American Plastic Molds are the key components used in making plastic products. From water bottles to toys, this process touches every facet of our daily lives.
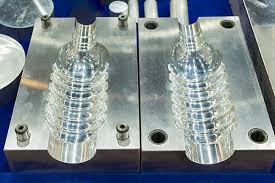
To make a plastic product, the first step is to design the desired product using computer-aided drafting (CAD). Then a mold is created. There are several types of plastic molding processes.
Known by the acronym rotomolding, this process produces hollow plastic parts with uniform wall thicknesses and density. It is especially useful for large-scale cases, munitions cases, footlockers and industrial equipment carriers that need to be rugged for transport. It also works well for molded plastic bins and bulk containers found in material handling applications and food processing industries.
The rotomolding process starts by pulverizing the desired thermoplastic resin into a powder. It’s then loaded into a mold and sealed shut. The mold then rotates biaxially at a rate of less than 15 RPM until the polymer melts and evenly coats the inside of the entire cavity. A draft angle must be factored in when designing the product to ensure the proper distribution of heat during this heating cycle.
Molten plastic is injected into the cavities using a screw mechanism, which can be fine-tuned to vary injection pressure and other factors that affect molten flow speed. This ensures all cavities are filled up to 95% with molten plastic before the cooling cycle begins. The cooling phase is based on the wall thickness and the desired end-product features, and it can range from milliseconds to minutes.
Because the rotational molding process is low-pressure, it isn’t ideal for producing sharp threads like those produced by injection moulding. Designers must work with the limitations of this process to create a product that will be strong and durable. A high injection pressure, for example, can cause premature solidification in the channels of the mold and lead to defects.
A draft angle should be factored in when designing the product as it will help the molten plastic to transfer into the cavities quickly and easily. This will also minimize the time it takes for molten plastic to cool down and become solid.
A draft angle should also be taken into consideration when designing large flat surfaces and sharp corners, as these can obstruct the flow of plastic during the rotational moulding process. This could result in uneven coatings or bridging at these points. To avoid this, it’s usually best to add steps or recesses into these areas of the design.
Injection Moulding
The injection molding process is an excellent choice for producing large quantities of dimensionally consistent plastic parts. It can also be used for highly complex parts, or for components that require stringent dimensional tolerances. The design process begins with a CAD file that defines the desired part shape and specifications. The tooling phase follows, which creates a mold cavity. The mold can have features such as bosses for threaded inserts or fasteners, ribbed supports to add strength, living hinges where flexibility is required, snap-fit joints or friction fits to join parts, and draft angles on vertical walls to aid in ejection from the mold. Wall thicknesses should be as consistent as possible, while avoiding undercuts that increase part cost, and sharp corners that may be susceptible to stress or delamination.
The hopper is the container where raw plastic pellets are fed, and a reciprocating screw is located inside the barrel that has heater jackets around its periphery to melt the pellets into a molten state. The screw is driven by a hydraulic cylinder that applies injection pressure to force the melted plastic into the mold cavities. The injected plastic is then hardened by the heat of the mould.
An essential consideration during the injection moulding process is that there must be sufficient injection pressure to maintain the flow of molten plastic until the cavities are 95% filled. This is determined by the viscosity of the molten plastic, its shear rate, and the injection speed. Injection pressure must be balanced against the thermal expansion and contraction of the mould components, which can cause non-uniform stresses that result in distortions or even voids in the finished product.
Injection moulding offers many advantages, such as high precision and repeatability, a low cost per part, a wide choice of available plastics, and speed. Disadvantages include a higher initial investment and a longer lead time than some other processes. Also, the temperature of the plastic during curing can be a factor in surface quality and colouration. Some polymers, such as thermosetting materials, can not be reheated, but others, like the commonly used thermoplastics, can be remelted and reshaped numerous times without altering their physical structure, making them highly recyclable.
Extrusion Moulding
When it comes to manufacturing plastic products, different processes are used depending on the product and its purpose. Two of the most popular methods are injection molding and extrusion moulding. Both of these processes involve an initial investment in the molds, which impacts the overall cost of the finished product.
With this in mind, it is important to consider which process is right for your specific needs and budget. Let’s take a look at the advantages and disadvantages of each to help you decide which process is best for your next project.
The extrusion process is a continuous and efficient way to manufacture linear shapes, like tubes and pipes, in high volumes. It has lower tooling costs than injection molding and is better suited for long runs of the same product, thanks to its ability to produce consistent cross-sections. Additionally, it is able to work with a wide range of materials, including thermoplastics, polyethylene and polypropylene.
During the extrusion process, the granules of plastic are heated in a feeder section using compression and frictional heat to melt the granules into a thick liquid. This is then forced through a die into a continuous length of the final shape. Once it has reached its target size, the molten plastic is cooled and solidified.
Injection molding is a more complex process than extrusion, and therefore requires a higher initial investment in the creation of the molds. This often leads to a longer lead time between the design stage and when production begins, which can impact the overall efficiency of your plastic manufacturing process.
Injection molding also generates more waste in the form of sprues and runners, which are the channels through which the melted plastic passes before entering the mold cavity. However, much of this waste can be ground up and recycled, reducing the amount of material needed to create each new part. Additionally, injection molding produces three-dimensional parts with a high level of accuracy. This makes it a good choice for more detailed and intricate designs, such as automotive windshield wipers.
Casting
Injection molding is the most common plastic moulding method. It’s used to produce a variety of different types of products including bottles, caps and other household items. It’s also used to make car parts and is a popular choice for high-volume production runs.
The injection moulding process is one of the 5 methods used to manufacture a plastic part. It involves injecting liquid plastic into a mold and then pressing it into shape, resulting in the finished product. This method can be used for a wide range of purposes and is extremely cost effective.
A plastic moulding tool is the reusable or sacrificial shape that holds the molten material. Most plastic moulding processes require a pattern, except for those that use a die or a casting. Patterns are often made from a hard and durable material like aluminium or a more flexible polymer such as elastomers.
The clamping pressure, which is the pressure applied to hold the mold halves during the injection step, is a vital component of the injection moulding process. It must be carefully controlled to complement the applied injection pressure and ensure that the molten plastic flows into the cavity without causing flashes or other defects.
Injection moulding machines use a screw or plunger to force molten plastic into the mould cavities until they are 95% full. This is done at a rate that depends on the viscosity and shear rates of the molten plastic, as well as the size of the cavity. The injection pressure should be increased gradually to maintain a steady flow rate and to prevent premature solidification of the molten plastic in the mold channels.
Blow moulding is another type of plastic moulding process that uses a heated metal mould to create hollow-walled products. It is similar to injection moulding, but the plastic is injected into a heated metal mold and air is then blown in so that it presses against the walls of the mold. This is then cooled and the finished product is ejected from the mould.
Compression moulding is a form of plastic moulding that involves the liquid plastic being poured into a heated metal mold and then compressed together to give the finished product its shape. The resulting product is strong and can be a good replacement for broken metal parts.